まずは、生産活動について考えてみる。生産活動は、人(Man)・設備(Machine)・原材料(Material)・金(Money)のいわゆる生産の4Mを入力とし、品質(Quality)・コスト(Cost)、納期(Delivery)の3要素であるQCDに、生産量(Production)・安全(Safety)・意欲(Morale)を加えたPQCDSMを出力とする活動と考えることができる。投入と産出の比率が生産性であり、この生産性が高い活動が望ましい生産活動である。 金(Money)の代わりに、方法(Method)を加える場合もある。
しかしながら、品質・コスト・納期などの要素は、一般的にそれぞれのレベルアップには他者の犠牲を強いるというトレードオフの関係にある。例えば品質管理と原価管理について考えると、品質を高めるためには設備投資や人材の増員といったコスト増を必要とすることがあるし、コストを無理に低減すれば品質の低下に繋がる可能性がある。
総合技術監理を行う技術者は、それぞれの現状レベルを的確に把握し、品質・納期・コストなどがより良い状態になるように、生産性向上の視点などから最適なリソースの配分を検討し、さらにその検討結果に基づいてそれぞれの担当者に的確な指示を出す能力が要求される。
2.1事業企画と事業計画
事業における最も初期の段階が事業企画である。ここでは、事業目的や事業規模を明確化するとともに、事業の収支の予測を行うためのフィージビリティ・スタディ(実行可能性調査 ; FS)が行われる。
フィージビリティ・スタディの結果、事業の実施が決定されると、続いて事業計画が立案される。この段階では、製品やサービスの具体的な内容、必要な技術の調達方法(独自開発するか技術導入するかなど)、生産場所や部品調達先など、様々な内容の検討を行う必要がある。これらの検討には、経済性管理とは異なる観点が含まれることも多いため、ここでは大枠は定まっているものとする。すると次に、工場などにおいては、事業計画として生産計画が立案される。その役割は、要求された品質と数量の生産物を、適正な時期に適正なコストで生産することにある。
生産計画は、需要予測量や生産能力をインプットとし、生産量や労働時間などをアウトプットとする情報変換作業である。通常は計画期間により、総合生産計画(長期)、基準生産計画(中期)、資材所要量計画(短期)という階層的な生産計画システムを構築する。生産計画は、主として工場での製品製造を念頭においたものであるが、生産技術の高度化や製品サイクルの短命化の中では、どのような分野であっても、系統的な生産計画を持つことが不可欠となってきている。つまり、以下に示す計画と名称や詳細な手法は異なっていても、基本的な考え方は共通するものである。
総合生産計画(Aggregate Production Planning ;APP)は、生産計画の第1ステップであり、需要予測量が重要なインプットとなる。生産設備などの制約の下で需要予測量と生産能力の差異を調整することになるが、具体的な実行計画とするためには、より短い期間に対する計画が必要である。
基準生産計画(Master Production Schedule ; MPS)では、最終製品毎の生産能力に対する調整を行うが、最終製品は部分製品や部品から成り立っているのが通常であるため、これらの部品類に対する生産・調達計画が必要となる。
資材所要量計画(Material Requirements Planning ; MRP)は、半製品(部分製品)や部品に対する生産・調達計画に対応する計画である。在庫データや購買データを用いて、製造部品の生産量や生産時期、購入部品や原材料の購入量と購入時期などを計画する。
2.1.1 フィージビリティ・スタディ
企業などの組織において、市場からの要求(ニーズ)、新規の技術やサービスなど(シーズ)に基づいたアイデアや具体的案件が提起されると、それを具体化するための事業企画を行う。このときに、事業として成り立つかどうかを判断する情報を収集・分析し、実行可能性を評価する活動をフィージビリティ・スタディ(実行可能性調査 ; FS)と呼ぶ。
フィージビリティ・スタディとして行う調査の内容は以下のようにまとめる。
(1)事業内容の具体化
事業の目的に沿って事業規模などの事業のフレームを具体化し、関係者のコンセンサスを得る。
(2)予備的調査と需要予測
統計資料などの既存資料を活用した調査や、アンケートやヒアリングなどによる市場調査を行い、事業化した場合の需要を予測する
(3)予備的な設計・試作
建造物やプラントなどの大型プロジェクトでは、予備的な設計によって建設に要する概略の期間やコストを予測することが行われるが、それと比較して小規模の設備や製品を生産するプロジェクトでは、実際に試作することも行われる。
(4)事業の収支予測と資金調達
プロジェクトを実施する際に必要となるコストと需要予測とを比較し、事業の収支を検討する。また、資金の調達方法の検討も行い予算規模が算定される。
2.1.2 総合生産計画
総合生産計画(Aggregate Production Planning ;APP)は、生産計画の第1ステップに位置するものであり、大日程計画といい換えることもできる。その基本的な目的は、需要予測量と生産能力を合理的に均衡させることである。通常は6カ月~18カ月程度の期間に対して、需要予測量を満足するために、生産率、労働力水準、在庫水準、残業時間、外注率などを調節して生産量と生産時期を決定することが行われる。総合生産計画は期中のコスト最小化を目的とする場合が多いが、雇用水準の安定化や在庫水準の適正化も重要な要素である。
総合生産計画を作成する場合、需要変動に対する対応が最も重要な課題となってくる。
生産計画を立案するときに調整しうる項目には、大きく分けて生産能力調整と需要平滑化があるが、それぞれの項目を単独で用いるか、混合して用いるかは難しい問題であり、数学的アプローチが行われているが、経験や知識を活かすためにグラフやチャートを用いる方法も考案されている。
総合生産計画の立案は、通常次のようなステップにより行う。
(1)個々の製品の需要予測から、生産する製品全体の需要予測量を求める。
(2)需要予測量を満足するために必要な労働力、在庫、残業、外注の各量を求める。
(3)需要予測量を満足し、目的(コスト最小化など)に合致した計画案を決定する。
この検討では、様々な代替案を試行錯誤しながら決定していく。
需要変動に対する生産計画の調整項目
生産能力調整
在庫水準調整
少需要期の在庫積上、高需要期の在庫放出
諸費用増加、繁忙期のバックオーダ発生、リードタイム長期化
労働力水準変更
労働者の雇用、解雇による生産率調整
教育の必要性、労働者モラル低下
生産率変更
残業や遊休による労働時間調整
残業には割増賃金や労働者疲労が発生、遊休は採用し難い
外注対応
一時的な需要増大を外注により対応
コスト高、競合相手への機密漏洩、信用ある外注先の確保難
パートタイマー活用
熟練を要しない作業に対する利用
損失を招く場合もあり
需要平滑化
需要増大
広告宣伝、販売促進キャンペーン、価格切下げによる購買喚起
莫大な費用と支出
納期遅延
バックオーダ(偶然もしくは故意による納期遅れ)
顧客の信用失墜、販売チャンスの損失
補完製品開発
季節性製品の開発
現実的には困難が伴う
2.1.3 基準生産計画と資材所要量計画
基準生産計画(Master Production Schedule ; MPS)は、総合生産計画によって生産する製品全体の生産計画を、最終的に製品アイテム単位のものへと分解することがその機能となる。
総合生産計画から基準生産計画へ分解する第1ステップでは、製品ファミリー(共通の段取りコストを持つ製品アイテムのグループ)単位の生産計画に分解することが行われる。この分解は、全計画期間中の一部の期間(通常は数ヶ月程度)を対象として行われるが、製品全体の生産量と製品ファミリーの生産量の合計を一致させる整合性と計画の実現性に注意する必要がある。また、コスト最小化の概念に基づき、段取りコストと保管コストを考慮して、製品ファミリーの生産ロット(またはバッチ)サイズを均衡させることも重要である。
分解の第2ステップでは、各製品ファミリーを製品アイテム(色・装飾・サイズなどがそれぞれ異なる特徴を持つ品目のグループ)に分解することが行われる。この際一般的には、製品ファミリー毎の生産間隔を可能な限り長くし(一つの製品ファミリーの連続生産)、個々の製品アイテムの在庫水準をある一定量に保持することに留意される。
資材所要量計画(Material Requirements Planning ; MRP)は、総合生産計画による製品全体の生産量決定、基準生産計画による製品ファミリーへの分解と製品アイテム毎の生産量決定を経た後に、製品アイテムを構成する部品や原材料の生産や調達を決定することがその機能である。通常は、1日から数日または週単位の計画となる。
資材所要量計画による個々の部品や原材料の生産量や購入量の決定を行うためのインプット情報には、基準生産計画の他に次のようなものがある。
(1)製品構成(Bill of Material ; BOM)
一つの製品アイテムを生産するのに必要となる部品や原材料を記したファイル
(2)リードタイム
購入部品や生産部品の発注時期を確定するために算出する、各部品の待ち時間、移動時間、段取り時間などの生産や調達に必要な見積り時間
(3)手持在庫量(在庫データ)
実際に在庫されている資材の量であり、不測の事態に備えた安全在庫や他への使用割り当て資材を含むが、オーダ中の資材は含まない
(4)受入確定量(購買データ)
計画の所定の期に受け入れが確定している資材の量
資材所要量計画は、通常コンピュータ化されたMRPシステムにより管理される。
MRPシステムの目的は、必要な量だけを生産し、余分な量を生産しないことである。
そのため、まず各々の製品アイテムと関連する部品に対して総所要量を計算し、手持在庫量と受入確定量から正味の所要量を算出する。この過程で、生産部品や購入部品の指定日における総所要量を満足するためのオーダ(正味の所要量相当分)発注時期が決定される。計算結果は、各種のレポートとしてアウトプットされる。
以上のような、生産計画を含む企業の基幹業務を支援する統合業務システム(Enterprise Resource Planning ;ERP)の概念に基づくパッケージ化されたシステムが広く使用されている。ERPは企業全体の経営資源を有効に総合的に計画、管理し、経営の効率化を図るための手法概念である。受注から納入までの一連の業務のみならず、会計・財務・販売・人事なども含むものである。
また、最近ではCALSとよばれる生産・調達・運用支援統合業務システムによって、供給業者、系列製造業者、流通業者、販売業者などを結び付け、開発・設計から生産、保全、流通まで製品の一生に関するデータを電子化し、迅速な情報交換・遠隔生産・電子取引を行う取り組みも始まっている。
参考:日本技術士会
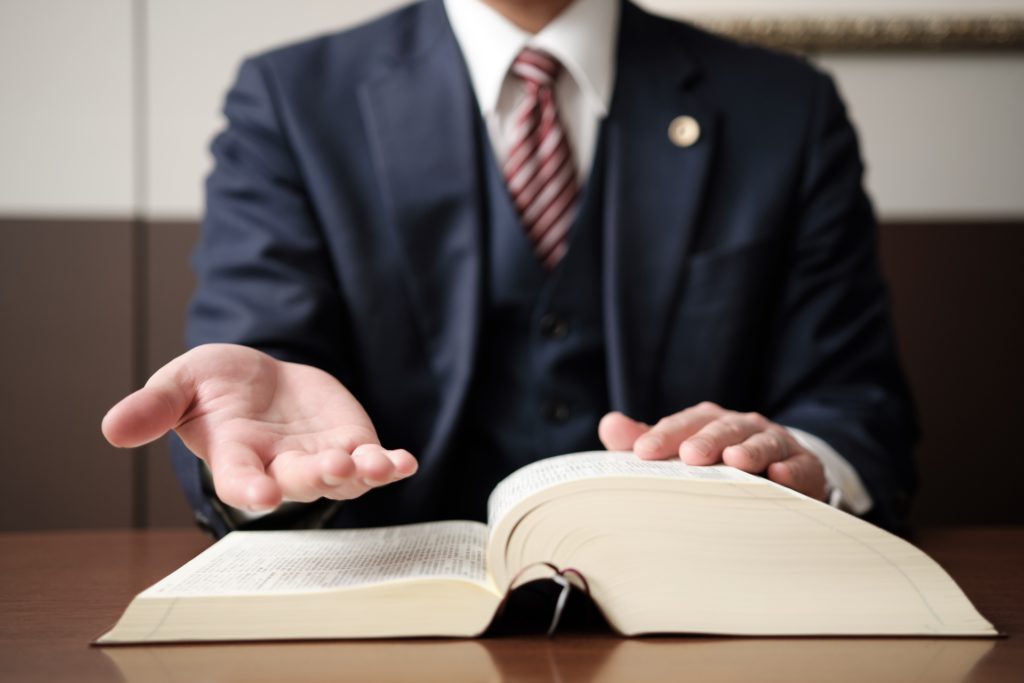