2.3 工程管理
事業計画に基づき、工場での製品生産や土木工事などを実施していくためには、生産活動を統制する必要がある。工程管理はそのための管理技術であり、主な目的は、事業計画に従った生産を実現することによって納期を遵守することにある。もちろん、製造品質の確保やコストの低減なども重要な項目であり、対象から外れている訳ではないが、それらに対しては別の管理技術が適用される。
工程管理の役割は、生産活動の時間的効率化と時間短縮化が中心であり、以下のような内容が含まれる。
(1)納期遵守
(2)生産期間短縮
(3)設備・人員の稼働率向上
(4)生産活動安定化
(5)操業度維持と生産量達成
工場などでの工程管理の対象は、生産計画によって製造現場毎に与えられる製造命令 (オーダ)と、各職場における製造作業の実行主体である作業部署である。オーダが投入されてから複数の作業部署を経由して完成するまでの流れを時間的側面から管理することが工程管理であると言える。生産活動における活動の最小単位は作業と呼ばれ、付加価値の源泉である。この作業を設計、計画、実施、統制、評価していくことは、作業管理とも呼ばれる。工程管理との関係では、作業標準と標準時間を資料化することが重要な内容であり、工程管理のみならず、原価計算などにも使用され、企業経営における最も重要な情報の一つと位置付けられる。
なお、建造物やプラントを建設する場合や土木工事などでは、工程管理を施工管理もしくは工事管理と呼ぶが、必要となる技術は基本的に共通するものである。プロジェクトの進み具合を定期的に把握し、問題があれば是正措置を講じるといった着工後の活動は、進捗管理とも呼ばれる
2.3.1 手順計画
手順計画における手順とは、生産活動を行うための作業順序のことである。手順は、負荷計画や日程計画においても必要な情報であり、仕事量や日程を検討するための基礎情報となるものである。
手順計画の目的は、次の3つに集約される。つまり、最適な生産方法の決定、生産方法の標準化、作業の適正分担である。その作成にあたっては、基本的に工程計画の作成と作業計画の作成という2段階の処理になる。工程計画では、オーダ毎に必要な作業と手順を設定し、部品や原材料から製品を生産する過程を工程表として具体化する。また、生産に必要な設備があれば、その種類などの選定を行う。次の作業計画では、各工程における作業内容の詳細を作業標準として作成するとともに、標準時間などの作業実施にあたって必要となる資料を作成する。実際に手順計画を作成する場合に、その手順の実現手段の主要素となるのは生産の4Mであり、信頼性、経済性、迅速性などを勘案して最も優れた手順を選定することになる。
なお、作業標準とは、作業条件、作業方法、管理方法、使用材料、使用設備、その他の注意事項などに関する基準と定義される。実際の作成にあたっては、マニュアル化されている場合が多く、その場合は定型化したフォーマットに記載することになる。 標準時間とは、一定の条件の下で、作業標準などにより標準として定められた作業方法で、標準的な作業能力を持った作業者が、標準の作業ペースと余裕を持って、作業を完成するのに要する時間のことである。標準時間は、稼動作業時間と準備作業時間に分けられ、各々はさらに正味作業時間と余裕時間に分けられる。これらは、稼動分析によって作業を稼働要素と余裕要素に分けることにより算出されるものである。
工程編成の目的は稼働率の最大化ということであるが、より具体的に目的を設定すれば、次の2つで表現できる。
(1)作業者数最小(サイクル時間固定の場合)
(2)サイクル時間最短(作業者数固定の場合)
2.3.2 負荷計画
負荷計画は、工数計画もしくは余力計画とも呼ばれ、日々変動する生産要求により必要となる仕事量(負荷工数)と処理可能な仕事量(能力工数)を均衡させるように調整する機能である。調整を行うための具体的な対策には次のようなものがある。
(1)負荷不足の場合
① 人員や設備の削減
② 就業時間の短縮
③ 生産部署の変更(他部署からの振替)
④ オーダの投入時間の前倒し
(2)能力不足の場合
① 人員や設備の追加
② 就業時間の延長
③ 生産部署の変更(他部署への振替)
④ オーダの投入時間の後倒し
負荷工数と能力工数は、作業者労働時間または機械運転時間を基準として計算することが一般的である。また、負荷と能力のバランスを評価する指標として、負荷率が用いられる。最適な負荷率は100%であるが、現実的には様々な変動に対処できるようにある程度の余裕を持たせることが重要である。
(1)労働時間基準
① 負荷工数=標準時間×生産数十段取り時間
② 能力工数=就業時間×(1-間接作業率)×作業者数×出勤率
(2)機械運転時間基準
① 負荷工数一標準時間×生産数十段取り時間
② 能力工数=運転時間×(1-故障率)×機械台数
③ 負荷率(%)=(負荷工数)/(能力工数)×100
負荷計画は、以下に示すステップによって決定していくことが基本であり、問題が生じた場合は前のステップに戻って検討し直す。
(1)各オーダの作業部署への割付け
(2)各オーダの作業日程の決定
(3)作業部署での負荷率の決定(算出・調整)
また、作業部署の稼動を安定化させるため、投入日程の前倒しや後倒しによる日々の負荷の平準化調整が行われる。そのための手法として、山積み・山くずし法があるが、最近ではPERTなどとともに汎用ソフトウェアにも組み込まれ、広く利用されている。
計画通りの生産を実現するためには、リードタイム(加工時間+段取り時間+停滞時間+移動時間+作業時間)を安定させることが重要である。リードタイムの中で最も長いのは一般的に停滞時間であり、作業時間がリードタイムの10%以下となる場合もある。負荷と能力のバランスが変化した場合は、投入量や産出量を制御し、リードタイムを安定化させることが重要である。
2.3.3 日程計画
日程計画は工程管理における計画の中心であり、計画対象の範囲や計画の単位の詳細さにより、大日程計画、中日程計画、小日程計画に区分される。
大日程計画は、6ヶ月~18ヶ月程度の期間に対してトップダウン方式で決定されることが多いものである。生産計画においては、総合生産計画に相当するものである。
中日程計画は、納期や稼動率を管理するための中核となる計画であり、1ヶ月~3ヶ月程度の期間に対して、部門別に作成されるものである。しかし、具体的な実行指示のための計画としてはさらに詳細化する必要がある。
小日程計画は、部品の納入状況や職場の作業実施状況などを考慮して作業部署毎に1~10日程度の詳細な計画として作成するものである。小日程計画では、中日程計画において指定された、投入日と納期日などのオーダを前提とし、作業部署毎の日程を設定することが行われる。これをスケジューリングと呼ぶ。また、さらに詳細な計画を立てる場合は、作業部署内の設備や作業者毎に仕事を割り付け(ジョブ・スケジューリング)、いつ、何を、どれだけ、どうやって作業するかを具体的に指示することが行われる。
スケジューリングを行うための手法には、次に示す日程展開方式と作業順序付け方式とがある。
(1)日程展開方式
生産の流れに従って作業の終了日程を決定していくフォワード・スケジューリングと、生産の流れを逆に辿り完成物の納期から順次工程を遡って作業の開始日程を決定していくバックワード・スケジューリングがある。この方式では、工程間の仕掛をある程度認め、仕事の割付けや手順を現場の進行管理に任せる場合に適している。(2)作業順序付け方式
作業員や設備に負荷される全ての作業に対して作業順序を決定していき、全ての作業の作業時刻が決定されるまで生産の流れに沿って計算していく方法である。この結果は、ガント・チャート上に表される。この計算では、納期遅れ最小化、総所要時間最小化、稼働率最大化などを評価指標として採用することが多い。
2.3.4 進行管理
職場の各部門では、日程計画によって生産活動の詳細を計画し、生産活動を開始する、その実行を統制(通常は中日程計画レベル)するのが進行管理である。なお、プロジェクトにおいては進捗管理とも呼ばれる。進行管理は、作業手配と実績管理の2つに分けることができる。
(1)作業手配
作業部署において、作業に必要となる資機材、工具、図面の手配などの作業準備を行うこと、及び作業の性質や納期を考慮して個別の作業割り当てを行い、作業指示を与えることである。この中で、オーダ毎の納期達成と作業能率向上の2つの目的を同時に配慮し、設備や作業者に作業の割り当てを行うことを差立てと呼ぶ。差立ての結果を指示する帳票には、移動票、作業票、出庫票、検査票などがある。
(2)実績管理
生産活動の実行状況を把握し、予定と比較することによって問題点を発見し、作業手配と連携して対策を実施することである。ただし、問題が大きすぎる場合は進行管理における調整では不十分であるため、日程計画の変更を必要とする場合もあり得る。実績管理の主要機能には、進度管理、余力管理、現品管理がある。以下にそれぞれの内容を記述する。
① 進度管理
日程計画に基づいた作業の進捗を調査して判定し、遅れが生じている場合は対策を講じる。納期遵守が主要な目的であるため、作業の手配から完了までの流れを把握しておくことが必要である。基本的な進め方としては、まず進度を分析し、許容されるレベルか対策を講じる必要があるレベルかを判定する。対策が必要な場合は、日程計画を維持するために必要な対策を講じた後、その効果を確認することになる。
② 余力管理
作業者や設備の能力と負荷を調整して待ち時間を減らし、過負荷を防止することが目的である。進度管理が日程計画の進捗調整の面からの管理であるのに対して、余力管理は能力と負荷のバランスの面からの管理である。
③ 現品管理
仕掛品の所在と数量の管理のことである。つまり、現品の不良・変質・破損、紛失による数量不足の防止、運搬作業や保管作業の容易化を意図した管理である。
近年では、進行管理をコンピュータシステムによって実現する、POPシステム(生産時点情報管理システム;Point of Production System)を導入する事例が増えている。
生産現場で時々刻々発生する管理用データをその時点で捉えて情報処理し、進行管理のみならず、品質管理や生産計画などにも反映させているオンライン進行管理システムである。
2.3.5 JIT生産方式
JIT生産方式(ジャストインタイム)とは、仕掛在庫や部品在庫をできる限り減らすために、日本の自動車製造業が開発したものである。これは非常に優れた生産方式であったため、現在は自動車業界に留まらず、世界中のほとんど全ての製造業に普及している。
従来の生産方式では、部品にしても製品にしても、需要予測に基づいて生産量を決め、それを順に生産することで需要を満たしていこう、という考えで生産が行われた。これをプッシュ型生産方式という。部品ができ上がっていなければそれを使った製品は組み立てられないので、このプッシュ型生産方式では最終製品に対する需要が生じるかなり以前から部品の生産が開始される。これは大量の製品が確実に売れるときは良いが、需要に変動があるときには、既に作ってしまった部品や仕掛在庫が無駄になることが多く、効率が悪い。そこでJIT生産方式では、「必要な物を必要な時に必要なだけ生産する」という理念に基づいて、需要に一番近い最終工程から、必要な分だけを生産するよう前工程に順に指示が出される仕組みが考案された。これが「かんばん」を用いたプル型生産方式である。
かんばん方式というのは、簡単にいえば、次のような仕組みである。
各工程で使う各部品に対して「引き取りかんばん」を、作られる部品に対して「生産指示かんばん」を、それぞれ適当な枚数用意する。ある工程で部品Aを使用するとき、それに付けられていた引き取りかんばん(△)を外し、部品Aを生産している前工程へ持っていく。そこででき上がって引き取りを待っている部品に付いている生産指示かんばん(○)をはずし、かわりに持ってきた引き取りかんばんを付けて後工程へ持ち帰る。前工程では、はずされている生産指示かんばんの数だけ部品を生産する。こうすると、使った分だけ部品が生産されることになり、生産指示かんばんと引き取りかんばんの合計数しか仕掛在庫もしくは部品在庫を持たないで済むことになる。
このようなJIT生産方式は、生産のための時間を大幅に短縮し部品や仕掛品の在庫を極限まで削減できる。しかしその威力を発揮するには、この仕組みを一つの工場内だけではなく、その工場へ部品を供給する全ての部品メーカーにまで広げなければならない。
日本の自動車業界が成功したのは、このJIT生産方式を関連の会社全てにまで普及させることができたからである。
近年ではこの考え方をさらに発展させ、コンピュータによる情報伝達の即時性を最大限利用した新しい生産システムに移りつつある。 JIT生産方式の実現形態としてPOPシステムを採用する場合も多く、最近では認識率の高さとコストの安さからバーコードを用いたものも利用されており、さらにはICタグの利用も検討されるようになってきている。
2.3.6 サプライチェーンマネジメント
サプライチェーンマネジメントは、JIT生産方式の思想などを包括的に取り入れ、原材料の調達から生産、出荷、流通、販売、さらには回収までも、情報ネットワークを利用して一括管理し、その内容を生産計画の立案やマーケティングに活用することによって、効率的な企業活動を支援するためのシステムである。 SCMでは、近年その能力を飛躍的に向上させているコンピュータの能力を最大限に活用し、リアルタイムに近い形で入手した情報を基に需要予測を行って生産を調整することで、在庫を減らしコストを削減する。しかも単独の企業ではなく、関連した複数の企業が協力して一つの情報システムを管理運用し、その効率を究極まで高めようとする試みである。
SCMでは、顧客満足を最大にするように数学的モデルを組み上げ、それをオペレーションズ・リサーチの各種手法などを利用してコンピュータで解析することにより、最適な計画を立てる。このときの基本的な考えとなるのが制約条件の理論(Theory of Constraints ; TOC)である。これは、ボトルネックとなっている工程の能力を最大限生かすように他の工程を制御するという思想に基づいている。まずボトルネックとなる工程を発見し、この工程の能力をフルに発揮させるために、それより後の工程ではプッシュ型生産方式で生産活動を行い、それより前の工程ではプル型生産方式で生産を行う。
さらに、このボトルネック工程の直前の工程で何らかの原因で生産に遅れができたときのことを考え、この両工程の間にバッファを設ける。しかしその他の部分には極力バッファを置かない。この方法により、少ない仕掛在庫でボトルネック工程の能力一杯の生産が可能となる。
SCMは、単独の企業ではなく、複数の企業が共同で参加する点が画期的であり、また生産・販売情報を中核とした統合業務システムへの取り込みも見られる。業務プロセスの流れを統合的な視点から1つのビジネスプロセスとして捉え、企業や組織の壁を越えてビジネスプロセスの全体最適をめざす、戦略的な経営管理手法として捉えられている。
参考:日本技術士会
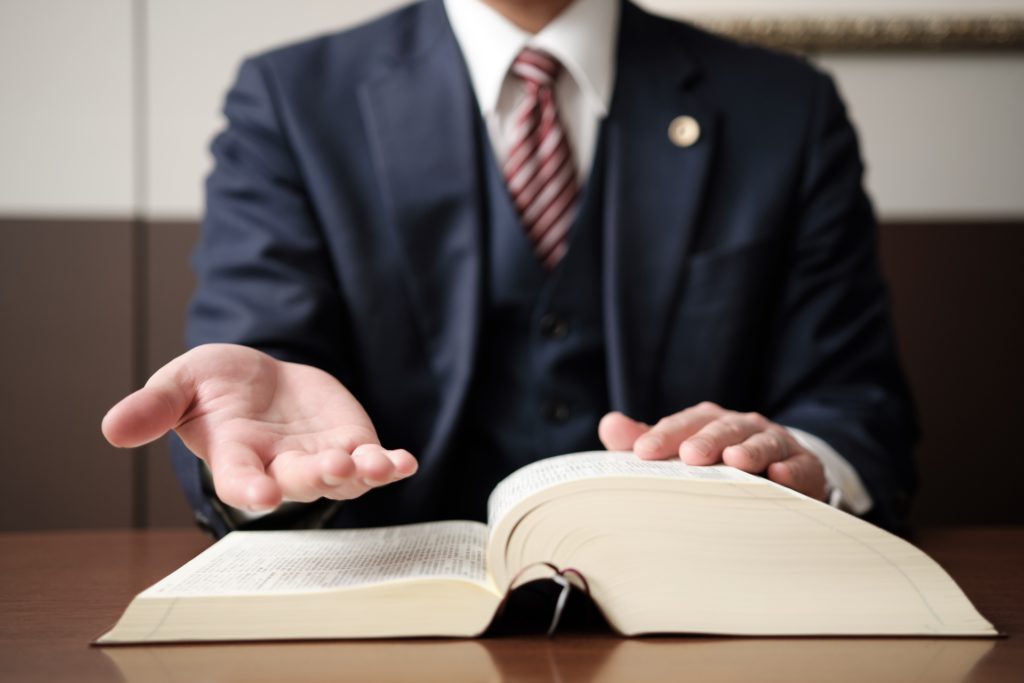